Juice doypack packing: 1 Delta robot completes 3-day work of 2 people in one day
Posted by:Administrator
Release time:2025-02-25
Keywords:doypack, casepacking, casepacker, deltarobot
Industry pain points: Traditional packaging mode encounters efficiency ceiling
In the juice beverage industry, stand-up pouch(doypack) packaging is widely favored by the market due to its portability and environmental protection, but flexible packaging forms pose severe challenges to automated packaging. The original production line of a well-known juice factory used manual packaging and faced three core problems:
Efficiency bottleneck: Manual packaging can complete a maximum of 1,800 bags per hour, which is difficult to match the capacity of the filling line, and there is a serious backlog of orders during the peak season;
Quality fluctuations: Manual operation causes bag wrinkles, leakage and other defects as high as 3%, and customer complaints are frequent;
Costs are rising: 10 packers are required for a single shift, and the annual labor cost expenditure exceeds 2 million yuan, and it faces the difficulty of recruiting workers.
The traditional production line is like an old steam locomotive. The filling section has been upgraded to high-speed rail speed, but the packaging link is still relayed by human push carts. The transformation and upgrading of the entire section is imminent.
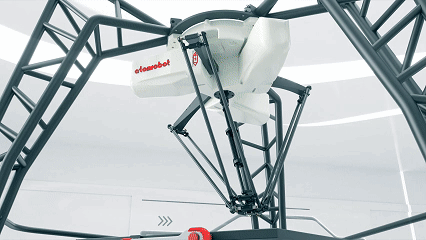
Solution: Customized solution for delta robot juice stand-up bag(doypack) by atomrobot
In response to customer needs,Atomrobot's technical team has created a three-in-one intelligent packing system of "high-speed visual tracking + flexible grasping + dynamic obstacle avoidance". The core of the project deployed 5 high-speed parallel robots(delta robot), with a single machine beat of 60 bags/minute and a repeat positioning accuracy of ±2mm. At the same time, the visual intelligent system is used to perceive and capture the bag posture (flat/tilted/stacked) in real time, and sensors are equipped to achieve accurate carton positioning and tracking; a dedicated end effector is used to independently control the vacuum suction cup group in different partitions to adapt to different bag types.
In terms of production line design, the principle of "logistics collaborative optimization" is adopted to make the material conveyor belt and the carton conveyor belt reversely arranged, shorten the robot's moving path, and integrate the three-channel diversion design to improve the overall processing density per unit area. At the same time, the suction cup pressure vision and sensor are used to monitor the grasping status in real time, and the intelligent error-proofing mechanism design of automatic re-grasping of missed suction is designed. When the robot misses suction, it will pause counting until the material is re-absorbed and then start counting.
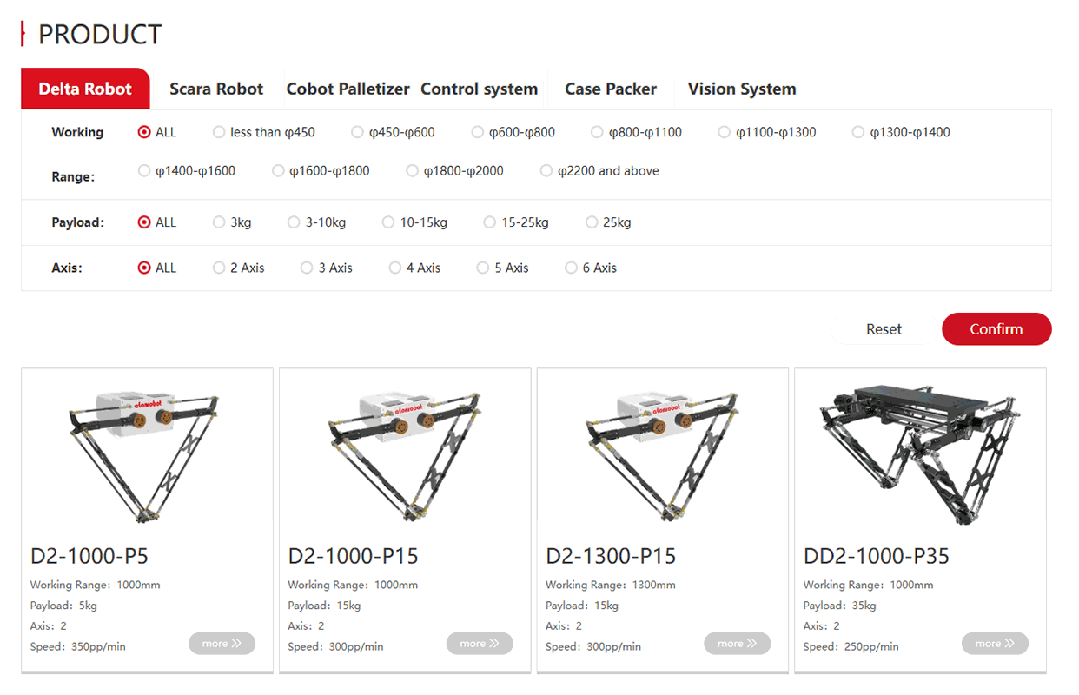
Implementation results: production efficiency has achieved a leapfrog value improvement
Compared with traditional manual packing, before the transformation, the hourly production capacity of a single manual line was 1,800 bags, the average daily processing order volume was 72,000 bags, and the packing defect rate exceeded 3%. After the automation transformation, the hourly production capacity of the machine line increased to 3,600 bags, and the average daily processing order volume expanded to 144,000 bags, an increase of 100% year-on-year, and the packing defect rate decreased by 99%. Based on the above structural optimization, the overall direct reduction of 10 people/shift saves about 1.8 million yuan in labor costs each year, and the annual material savings brought by packaging loss exceed 500,000 yuan, with direct explicit benefits-manpower and material cost savings of 2.3 million yuan.
At the same time, the implicit value is obvious: the overall delivery cycle of juice stand-up bags has been shortened by 40%, and customer satisfaction has been improved by 27%; after the automation transformation, the equipment footprint has been reduced by 15%, leaving enough space for subsequent production line expansion.
Compared with the explicit and implicit values, the comprehensive investment return cycle of this project is only 12 months.
"The atomrobot's delta robot not only brought a breakthrough in production efficiency, but also reshaped our quality control system. Now the packing status of each batch of products can be traced, which is a key plus point for passing ISO 22000 certification," said a project manager of the factory. "At the same time, the robot's 24-hour stable output has solved the most troublesome night shift scheduling problem in the past. Our staff can safely focus on process optimization..."
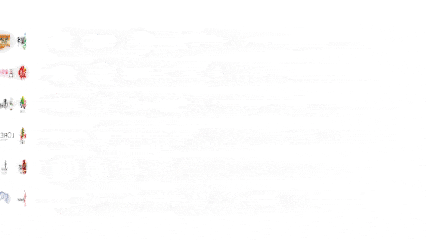